The cost of replacing commercial equipment, the type that is built once a manufacturer receives a purchase order, following smoke or water exposure can be extremely high. Putting aside the cost of the equipment itself, replacement also results in prolonged operational downtime, which in turn leads to lost revenue, at times employee furlough, and customer loss to competitors. In some cases, wholesale replacement – especially for custom equipment – can take between 12 and 24 months and cost millions of dollars.
At the end of the day, whether you’re an insurance adjuster or a business owner, the goal of minimizing production downtime and business interruption is at the top of the priority list. This is when alternative options to replacement, such as technical equipment restoration, are critical to understand.
Starting with the Basics – What is Restoration?
Hurricane debris, fire extinguishing effluent and other contamination events can cause foreign particulate to settle on sensitive electronic components and mechanical assemblies, which can adversely affect their operation. Depending on the type of contaminant, the effects can vary widely. The process of equipment restoration starts with a professional recovery firm inspecting the equipment, analytically quantifying the existence or absence of loss related contaminants, and conveying triage recommendations in addition to preservation options. Equipment that qualifies for technical recovery would be disassembled, decontaminated, reassembled, and prepared for testing, repair, and recalibration.
Professional decontamination would restore the equipment to its original design cleanliness specification. Analytical samples are harvested to quantify the success of the decontamination, thereby also instilling certainty that warranties and service contracts can remain intact. While equipment that did not experience a loss often fails before the end of its useful life due to a lack of preventive maintenance, restored equipment is expected to meet or exceed its life expectancy, as long as routine maintenance is performed.
The Benefits
Reduced Downtime
When considering risk management best practices, it may seem obvious that companies would have more than one supplier for everything they outsource or purchase. Doing so ensures that regardless of what may happen to a supplier, their production will be minimally impacted. However, many companies do not have a second supplier and may be dependent on a vendor that sustained a loss. While the insurance carrier will make the vendor whole, paying for restoration or replacement of equipment and perhaps business interruption, if this process is prolonged and their clients start to second source the same parts or even switch to a different vendor altogether, the business may never recover.
The lead time to secure new equipment can take months, and in the case of custom equipment, sometimes even years, resulting in prolonged business interruption. Equipment restoration has proven to be a much faster way to get businesses back in production. To illustrate this, let’s look at a real-life example.
In Mexico, heavy rains caused a river to overflow and sent feet of muddy water into the campus of a large auto plant. Equipment was waterlogged and contaminated with dense debris. Replacing all of the affected equipment, most of which was custom, would have quite literally taken years. Even though restoration was performed, the company still booked a $442 Million loss in the short period of time it could not manufacture cars. Imagine the cost if they had to wait for replacement items.
In another example, product in a heated high-pressure machine caught fire and contaminated surrounding equipment. The event, which took place at an Ohio chemical plant, activated the sprinkler system. The chemical plant’s engineers condemned a number of electrical control panels, although they recognized that replacement would have taken six months. Waiting for replacement panels would have reduced the plant's production capacity and resulted in shortages to fulfill existing orders. Through technical reconditioning, they were back in business in a fraction of that time and all orders were shipped as scheduled.
Lowered Costs
Getting straight to the point – restoration, in most cases, is going to cost less than replacement. You may be thinking that it very well should be given that the equipment is not being replaced. However, there are multiple factors to consider when performing a cost benefit analysis. As noted above, the goal of minimizing production downtime is at the top of the priority list. From an indemnity perspective, at times the expected claim from business interruption can be far greater than the cost of the equipment and the building combined.
Consider the following scenario – even as this blog post is being authored in 2021, there are still computers that control machinery while operating on a disk operating system (DOS) platform. DOS existed before Microsoft Windows and phased out in 1994. When these computers fail, or are involved in a loss, the equipment owner is faced with costly options. It may seem logical to simply replace the computer with a $800 Windows 10 version, although doing so is easier said than done. The computer communicates with other electronic modules or control cabinets. The computer and the control cabinets need to have a common communication platform. Once something is upgraded, it could trigger upgrades for everything else. What started out as a potential $800 replacement will end up costing hundreds of thousands. This means that if for some reason technical restoration of the computer, as an extreme example, would cost $2,000, compared to the hundreds of thousands saved, the restoration cost still makes sense. Typically, however, the cost of replacement compared to equipment restoration can range from 50 percent to as little as five percent of the total replacement cost.
Let’s dive into two real-life examples to help illustrate the cost savings –
A large university suffered a fire in an electrical panel. After considering their options, they opted for restoration. By doing so, approximately 1,200 devices were successfully decontaminated in 60 days, and over $39 Million was saved in replacement costs. All of the warranties and service contracts remained intact.
A church in Texas sustained damage from a fire that started in a sound booth. A sizeable portion of the main sanctuary needed to be demolished and reconstructed. The fire caused the church to lose their online streaming capabilities, which they were doing weekly during the COVID-19 pandemic. Six-hundred items were inventoried and 550 of them could be decontaminated including audio/video equipment, stage lighting, office equipment and musical instruments. Restoration enabled streaming and services to resume the following Sunday, and once everything else was addressed, about $500,000 was saved.
Equipment Warranty
Most manufacturers don’t revoke warranties immediately following a loss. One of the reasons is that unless a piece of equipment was fairly new, a warranty didn’t actually exist. That does not stop the warranty discussion from taking place as though a warranty did exist, as equipment owners need to regain a sense of confidence that their equipment will not fail as a result of the loss. Manufactures often advise that they do not provide disaster recovery services. As such, replacement seems like the only option from their perspective.
When educated about decontamination processes that would restore equipment to the designed cleanliness specification, manufactures do appreciate the technical nature and scientific approach of the proposed restoration. Manufactures may have a technician present during the decontamination phase, or simply request a copy of the final analytical cleanliness data. Either way, whether a warranty exists or a service contract, by engaging the manufacturer or third-party service provider before restoration commences, there is a great deal more willingness to help the equipment owner recover as quickly as possible and warranties are not revoked. If for some reason the warranties were revoked before the collaborative process took place, they are far more likely to be reinstated following the decontamination, testing, repair, and recalibration.
Insurance Premiums
There is a general misconception that insurance premiums automatically increase when an insurance company pays for a covered loss. The reality is that multiple factors go into rate increase considerations. Such factors include claim type, amount paid, the number of claims during the policy period (also known as claims history), projected severe weather impacts, cyber and data risks and many others. When business owners are faced with potential rate increases, two options become clear, unless the business owner feels that their current insurance company is simply the best regardless of cost. The first option is obtaining competitive bids from other insurance carriers. The second is taking on more risk by increasing their deductible.
While equipment restoration first and foremost helps the equipment owner minimize production downtime and business income loss, it also helps manage the claim settlement amount. As long as a business presents a reasonable risk, an insurance company will continue to extend coverage albeit with a potential rate increase if the claims history and overall amount paid is higher than originally considered by those who priced the risk (insurance underwriters).
If you had an incident and need help assessing the true extent of the loss scientifically, contact an AREPA specialist. We can help differentiate between equipment that can immediately resume production and create a triage plan for items that may need to be decontaminated, tested, and repaired. Regardless of insurance proceeds, claim history, or deductible, ensuring your customers’ needs are met is the top priority. To find out more, check out these case studies and see what AREPA can do for you.
ABOUT THE AUTHOR
By: John Hartlieb
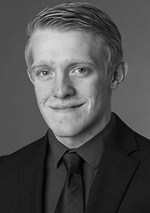
As an experienced professional in the field of electronic manufacturing, John draws from his background to effectively evaluate high-tech electronic, electrical, and mechanical equipment that was impacted as a result of fire, water or other contamination event. John currently serves as a project manager on large scale assignments where his responsibilities include assessment and decontamination of medical, electronic, industrial and manufacturing equipment, supervision of restoration specialists and contractors, and technical testing / repair, where applicable, to ensure that production can resume with minimal downtime.